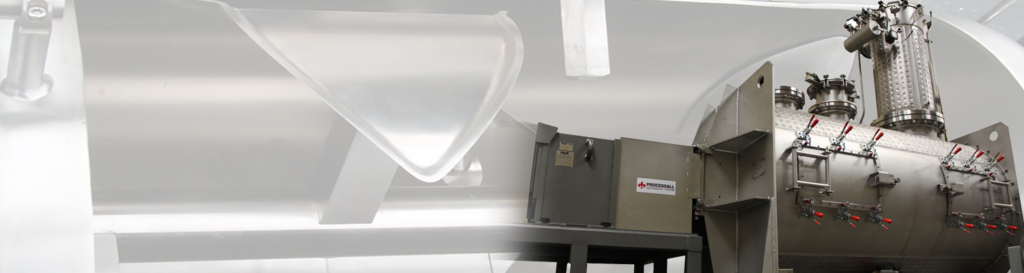
Agglomeration/
Wet Granulation
The process of combining smaller
particles into larger sized agglomerates
The agglomeration process usually produces an open,
more porous particle structure and is often desirable for these reasons:
• The larger and more uniform particle size distribution improves the flow and handling properties of the product for better tableting, briquetting, package filling, extrusion, or powder compression.
• Agglomeration increases product dispersion and solubility.
• Granulation often changes the bulk density.
• Product “dusting” can be controlled by agglomeration
The correct moisture level, an appropriate binding agent, or solubilizing agent to control surface tension can all be used to affect particle size and density. Conventional spray and fluid-bed granulation techniques require heavy capital investment, involve elaborate and time-consuming clean-up, do not readily handle materials with different bulk or particle densities, require a large amount of floor space, and often need the expense of post-granulation drying equipment.
Typical Agglomeration/Wet Granulation Sequence:
Typical Agglomeration/Wet Granulation Curve
In Processall’s Mixmill® line of mixing granulators, medium-density blending elements lift and disperse the product to produce a mechanically fluidized bed. This rapidly and efficiently blends materials of widely different density and particle size. Meanwhile an integral, high-intensity chopping mill system distributes the agglomerating solutions while binding and controlling particle size. Post-milling is usually unnecessary.
The high efficiency of the chopping mills often permits using less granulating solution and eliminates the need for subsequent drying. When post-drying is necessary, a Processall Mixmill® equipped with a heated jacket takes advantage of the excellent heat transfer rates of the fluidized bed systems to rapidly and efficiently dry the agglomerated product. Processall can provide a complete vacuum drying system with a solvent recovery/reuse capability.
Vacuum drying after pharmaceutical granulation in a Processall Mixmill® improves particle size distribution reproducibility. Processall maintains a well-equipped
testing laboratory and a rental fleet dedicated to process and development requirements.
Typical Applications
Food:
Food products are frequently agglomerated to increase their
dispersion rate in liquids. Fruit and chocolate drink mixes, for example, must “dissolve” quickly with minimal stirring.
Pharmaceutical:
Pharmaceutical granulation produces the material handling
characteristics and absolute uniformity of die-fill needed to assure rigid dosage accuracy on high-speed tableting presses.
Chemical:
In the chemical industry, agglomeration controls dusting of such materials
as fly ash, fertilizer, and other hazardous powders.
Ceramics & Powdered Metal:
Powdered metal and ceramics processors granulate to prevent
component segregation, improve material flow, and adjust density to modify
die compression ratio.