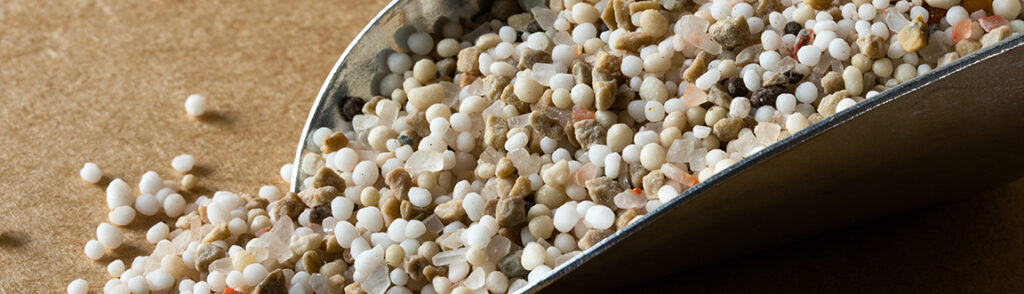
Chemical Applications
In the chemical industry, Processall equipment performs several unit operations in one process vessel, saving capital cost, floor space, and operating time, while improving product quality
In the Processall design, medium-intensity mixing elements lift and blend the product in a “mechanically fluidized bed” action. The independently operated chopping mills add high intensity shear to the product. The combined mixing and milling action of the Processall Mixmill is exceptionally well-suited to processing a variety of hard to handle liquids, powders, pastes, and slurries. It allows processors to take advantage of the excellent heat and mass transfer characteristics of a fluidized bed. The Mixmill design can be adapted for high pressure reaction, filtration, and vacuum drying. Processall provides a complete customer service lab and maintains a rental fleet for clients’ process and product development requirements. Production units have capacities ranging from 100 to 30,000 Ibs. Lab and pilot-scale models with 2 to 150 Ibs. capacity are available
3000HL Mixmill
Typical applications:
• Stearates
• Fertilizers
• Fire Extinguisher Powders
• Cellulose Derivatives
• Polymer Modifications
• Rigid and Flexible Plastic
Compounding
• Industrial Sludge and Waste
Application Highlights:
• Most fertilizers can be processed in a Processall Mixmill. To improve material handling and to reduce product loss caused by dusting, the product is agglomerated and dried in a Mixmill drier.
• Fire-extinguisher powders are coated with liquid anti-friction lubricants to improve flow and material handling. The fluidized bed exposes an extremely large particulate surface area. Liquid lubricants can be atomized and sprayed into the fluid bed to be
rapidly and uniformly distributed through the powder.
• High-pressure, vapor-phase polymer modifications followed by vacuum drying and devolatization are ideally suited to Processall
reactor/dryer systems.
• Rigid and flexible plastic compounding and master batching can be supplied as a complete turnkey system. This is to take advantage of the high power and rapid cooling capabilities
of the Processall Mixmill.
• Both liquid and solid metal stearates used in soaps or as additives in plastic pipe, electrical insulation, and vinyl siding can be made in Processall vessels. The (frequently liquid) reagents are mixed, chemically reacted, and dried to a free flowing powder in a single Processall reactor dryer. During the drying step, the fluidized bed action provides excellent contact of the particles with the heat transfer surface, while the integral, high-intensity chopping mills disperse and de-lump agglomerates formed as the product passes through the “pasty” stage. The final product can be sifted and packaged directly, usually without post-milling.
• Cellulose derivatives can be prepared at high pressures and dried under vacuum in efficient Processall Prestovac reactor driers.
• Industrial sludge and waste blending, dry power densification, and agglomoration are successfully performed in Processall equipment