Humans’ love of cacao predates written history in some parts of the world. The love of the cacao beans had Aztecs use cacao beans even as a form of currency. It was not until the 1600s did cacao reach the European shores and monks began to improve on the characteristics of the cacao bean. In the 1800s with the invention of the Dutch process to reduce the bitterness of cacao, modern chocolate exploded onto the scene, and we began to see the advent of the sweet nectar of the gods. Since then, the chocolate industry has quickly grown into a nearly 50-billion-dollar industry with players as small as the local “mom and pop” shops to multinational corporations like Hershey’s.
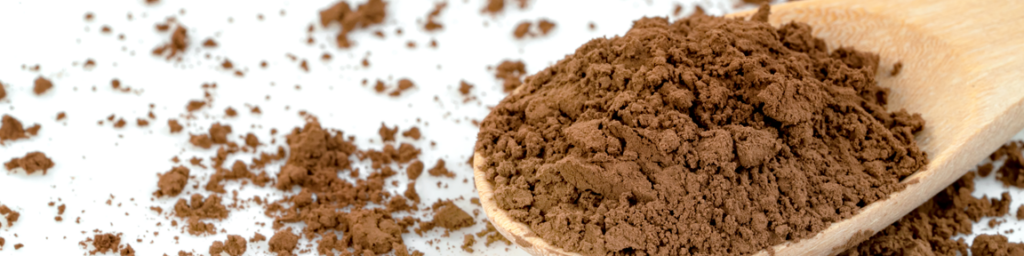
In the 1960s, plow mixing technology came onto the scene and many large chocolate manufacturers quickly adopted this technology. The chief reason for their switch to this technology is the versatility of plow mixers. Whether it be for performing the Dutch process of cocoa (an alkalization reaction), making compound chocolate blend, or plow mixing, this technology has been a part of the industry. Units for the chocolate industry have been customized to meet the tight requirements of this industry including the extremely tight clearances for the plow to drum.
Additionally, these units have been customized with the ability to automatically load all the dry powders and liquids into the system and prevent human contact. The mixer then creates a mechanically fluidized bed that converts the raw materials (cocoa powder, sugar, oils, and other optional ingredients) into one of nature’s purest delights.
Besides being able to do the blending and reacting, plow mixers often help in the sterilization of the product. It additionally has the capability to heat the ingredients due to the heating jacket on the vessel.
Processall employees have a long history of working with companies in all markets aiding in everything from initial testing to installation of the unit to maintenance throughout the life cycle of the unit.
Processall’s plow mixing technology gives manufacturers a leg up on the competition. Listed below are some of the benefits of moving toward plow mixing technologies for chocolate operations.
- Creation of a mechanically fluidized bed that reduces the mixing times
- A high heat transfer rate within the vessel enables faster drying
- The vessel jacket allows different media (hot oil, steam, or tempered water) to be used depending upon the thermal sensitivity of the product
- Adjustable pressure conditions enable both high-pressure applications and near-vacuum pressures to occur during different stages of the reaction
- Ability to serve as a reaction vessel for performing the Dutch-process cocoa reaction
- Customizable to include a pulse back filter to prevent powder clogging
- Offers mixing speeds up to 600% faster than ribbon blenders
- Can be designed to have extremely tight clearance of the drum to the head maximizing mixing of chocolate compounds
- Thermal jackets to allow for optimal temperature controls
- Ability to disperse cocoa powders, sugars, and other dry materials into oils and other liquid mediums to create compound chocolate
- Easy to scale up and predict mix and drying times after lab testing
- Vessels can be further outfitted to increase versatility:
- Mechanical seals – will allow the vessel to be pressurized as well as reach a low-vacuum (28 Hg)
- Liquid lances – allows media to be sprayed onto the substrate
- Ability to perform the reaction and the mixing and drying within one unit resulting in:
- Faster throughputs
- Reduced energy consumption
- Smaller footprint on the production floor
Areas Plow mixers aid chocolate manufacturers
- Sterilization operations
- Dispersing powders into liquids
- Reaction vessel for the alkalization reaction
- Drying material to make chocolate powders
- And many more
Processall maintains a fully equipped testing facility in Cincinnati, Ohio designed to provide customers with the data they need to develop their process, evaluate equipment, scale up, and identify the necessary equipment to maintain desired production volumes. We extend an open invitation to all potential customers to bring their products to our test center and get a “hands-on” experience with our technology and capabilities.
We also maintain a rental fleet that customers can utilize to do further testing at their facility or employ to minimize their startup costs for a new process.
Please feel free to contact us with all your material processing questions and our experienced industry professionals will help you find the right mixing solutions for your application.