Whether it be cathode paste for the battery industry, body creams for the personal care industry or adhesive blending for the construction industry, high viscosity materials, and their blending affect virtually everyone’s daily life. Since its inception, plow mixing technology has been at the forefront of this liquid blending market. These mixers were initially designed to aid in the pastry industry for high viscosity pastry blending. Due to their versatility, they were quickly found to be able to mix much more than culinary applications. Industries ranging from the mining industry to the composite material manufacturing industry to the nutraceutical industry now use plow mixers regularly for high viscosity mixing.
Plow mixing technology can perform many blending applications many lower shear mixers cannot do. The reason is they use a high horsepower engine and have mixer arms designed to maximize the mixing action which creates a mechanical fluidized bed. Although these mixers use high horsepower engines, they are still capable of mixing materials as fine as dried oats without damaging the material. Research has shown too that plow mixers mix fluids as thick as 600,000 centipoises with relative ease.
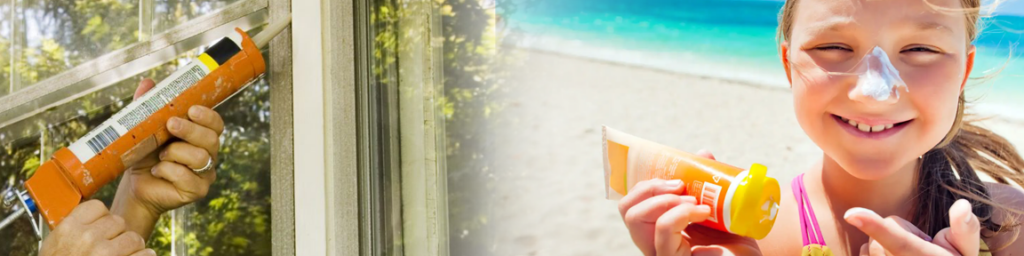
It is common for materials of these high viscosities to often act as non-Newtonian fluids and modifications to optimize mixing conditions sometimes need to be made. For this reason, Processall’s plow mixer can be customized to fit these unique challenges. Viscosity is known to be temperature dependent; therefore, to mix ultra-high viscosity materials, Processall’s plow mixers can be thermally adjusted with the heating jacket. Since viscosity also has a direct correlation to pressure, it is possible in some applications to mix higher viscosity materials at lower pressures to reduce viscosity in the system; however, limited work has been done on this so far. Processall’s plow mixer can be also outfitted with VFD controllers to adjust the engine speed to reduce energy consumption in the process.
Processall’s employees have a long history of working with the chemical industry aiding in everything from initial testing to installation of the unit to maintenance throughout the life cycle of the unit.
Processall’s Plow Mixing technology gives manufacturers a leg up on the competition. Listed below are some of the benefits of moving toward plow mixing technologies for high viscosity applications.
- High powered engine which causes high Froude number and reduces mix times
- VFD controllers to control the engine and prevent possible engine burnouts
- Vessel jacket allows different media (hot oil, steam, or tempered water) to be used depending upon the thermal sensitivity of the product
- Ability to adjust between high pressure and low pressure depending on the steps in the process
- Thermal jackets to allow for optimal temperature controls
- High-speeded mix which is gentle enough to handle materials as fine as dried oats without damaging the material
- Easy to scale up and predict mix, reaction, and drying times after lab testing
- Ability to handle viscosities as high as 600,000 cps without issues
- Vessels can be further outfitted to increase versatility:
- Mechanical seals – will allow the vessel to be pressurized as well as reach a low vacuum (28 Hg)
- Liquid lances – allows media to be sprayed onto the substrate
- Ability to perform the reaction, mixing, and drying within one unit resulting in:
- Faster throughputs
- Reduced energy consumption
- Smaller footprint on the production floor
High Viscosity Applications using plow mill technologies
- Food Processing
- Battery Manufacturing
- Personal Care
- Cosmetics
- Adhesive Technologies
- Agricultural
- Industrial Chemicals
- And many more
Processall maintains a fully equipped testing facility in Cincinnati, Ohio designed to provide customers with the data they need to develop their process, evaluate equipment, scale up, and identify the necessary equipment to maintain desired production volumes. We extend an open invitation to all potential customers to bring their products to our test center and get a “hands-on” experience with our technology and capabilities.
We also maintain a rental fleet that customers can utilize to do further testing at their facility or employ to minimize their startup costs for a new process.
Please feel free to contact us with all your material processing questions and our experienced industry professionals will help you find the right industrial mixing equipment solutions for your particular application.