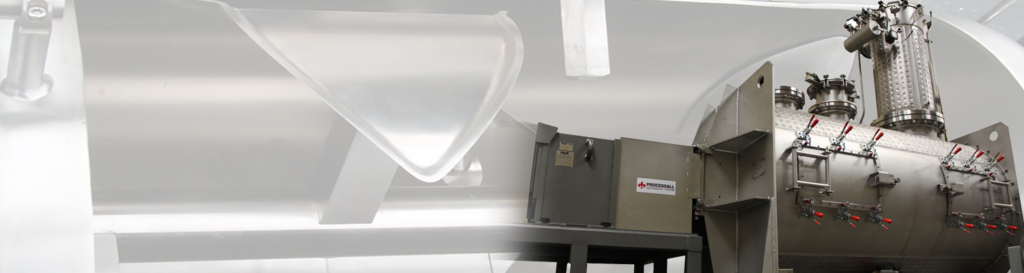
Horizontal Vacuum Plow Dryer
Drying touches many aspects of chemical manufacturing. Whether it be food production, pharmaceutical manufacturing, or even processes in the agrochemical industry, drying technologies are a vital part of the chemical production industry. This is because many chemical processes result in the formation of a wet filter cake. This cake typically must be purified and cleansed before it is sold to customers.
The initial precipitates are often full of impurities that form during reactions and these contaminates need to be removed following the filtration processes. The unrefined filter cake is often then exposed to several purification steps. Often the material is washed with different solvents to remove any excess byproducts or unreacted materials from the product.
These solvents range from a wide variety of organic solvents to water most often. After the purification stage is completed, many companies are then left with a solvent ridden material that needs to be dried. There exist a wide variety of drying techniques on the market like air driers, microwave driers, radiant heat driers and vacuum driers. However, few offer the speed, particulate size control, and customization features of plowshare vacuum driers.
Vacuum drying with plow mixer technology maximizes the heat transfer coefficient between the jacket and the product while lowering the product temperatures required for vaporization. See Figure 2 for an example of how much lower the boiling point is under Vacuum conditions. (24 in Hg and 26 in Hg are typical vacuum pressures one can achieve in plow mixer vacuum driers)
The vacuum drying process needs to take place in an appropriate vessel which can be heated and be placed under vacuum. It is for this reason drums used in vacuum drying must be carefully designed to stand up to the rigors of a multitude of temperature and pressures without damage. The vessel also needs to be capable of agitating the material in such a way as to maximize the heat transfer from the external jacket to the product. A properly designed vacuum drying unit can be heated with hot water, steam, or a heat transfer fluid depending on the product limitations all while withstanding vacuum pressures.
The vacuum dryer agitation also helps to eliminate or reduce the amount of agglomerated product assuring complete dryness and a narrower particle size distribution. While drying, most materials go through a heavy or doughy phase where large lumps are generated. Occasionally, these larger lumps hinder the drying rate because the liquid being removed must travel to the surface of these lumps. Due to the fact agglomerations can occur, plowshare vacuum driers can also be equipped with additional mixing devices called choppers that can impart shear to break up the large heavy lumps. They can break apart any agglomerates and help reduce the product particle size. (See Figure 3).
Still, most of the time plows high speed agitation alone prevents particulate agglomeration from occurring and preventing the need for chopper technology. It is always best to do laboratory testing with trained technical personnel to determine the best course of action when performing drying applications.
During the vacuum drying operation, the unwanted solvents can be removed as they exit the dryer as a vapor. The vapor rate can be quite large because of the good heat transfer and the vapor volume will expand as much as 15 times the liquid volume. Therefore, it is useful to have a set of filters to separate the generated vapor from any potential entrained solid product. To prevent the filters from getting wet with condensed vapor, the filter housing should be jacketed to provide heat input to maintain the vapor form. The filter can be cleaned by applied a pulsing mechanism that is directed down the inside of the filter dislodging any collected dry product. This type of filter unit is referred to as a pulse-back filter housing.
After reaching the final desired volatile content in the product, the material can be cooled for collection and final packaging without exposing the operator to dangerous conditions. Cooling of the product can also reduce the risk of fire or explosion by exposing the product to the atmosphere. The vacuum dryer can also be purged with an inert gas to further protect the product as well as the operator if the liquid being removed is a flammable solvent.
Processall’s Plow Mixing technology gives chemical manufacturers a leg up on the competition.
Listed below are some of the benefits of moving toward plow mixing technologies
for chemical manufacturers.
• High heat transfer rate with coefficients upwards of 50 BTU
(hr•ft²•°F) which increases the speeds of drying
• Lower vaporization temperatures protect thermally sensitive material
• Can be customized with a wide variety of safety
features to improve employee safety when handling dangerous materials
• Ability to serve as both a reactor and dryer of materials thus reducing the need for multi-unit operations.
(Many stearate manufacturers use plow mixers because
of these features)
• VFD motors enabling wide levels of control for the mixer
speed therefore better control of the particle size of the
dried material
• Can be customized to include pulse back filters to reduce
product loss during drying
• Thermal jackets to allow for optimal temperature controls.
• Ability to serve as a U1 pressure vessel