Many people believe carbon fibers to be a manufacturing miracle that lasts twenty years, however, initial work on this material reaches back over 140 years to the advent of the light bulb. Nonetheless, it was not until the late 1950s that high-performance carbon fibers became more prevalent in the manufacturing industry. The applications of carbon fibers now touch everything from green manufacturing to aerospace, to sporting goods. The reason for this is carbon fibers are a lightweight material that is also stronger than metals such as aluminum. With growth rates of over 10 percent annually, we are only beginning to see carbon fibers revolutionize our daily lives.
The blending of carbon fibers into materials is going to become increasingly important in the upcoming decade. Especially in the past ten years, the price per pound of carbon fibers has dropped over 1500 percent. It is going to become more vital for companies in this emerging technology to optimize their manufacturing methods. Plow mixing technology has a long history of dispersing everything from fabrics to pigments into materials. Due to the high-speed mixing action and dispersive capabilities, Processall’s mixers are ideal for distributing everything from rayon to carbon fibers into a multitude of mediums to create reinforced composite materials.
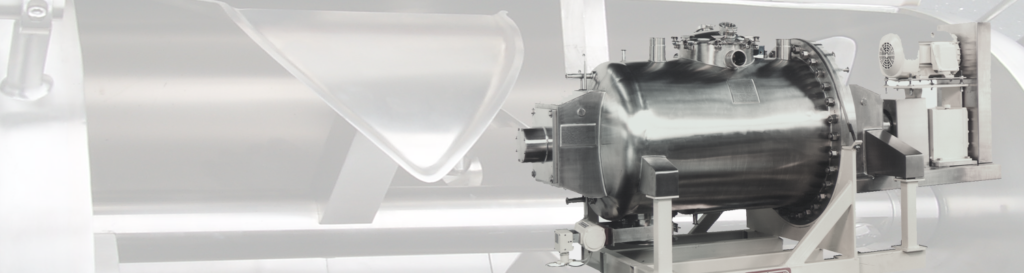
Processall’s employees have a long history of working with the composite material industry, aiding in everything from initial testing, to the installation of the unit, to maintenance throughout the life cycle of the unit.
Processall’s plow mixing technology gives manufacturers a leg up on the competition. Listed below are some of the benefits of moving toward plow mixing technologies for carbon fiber composite materials.
- Ability to disperse materials together creating greater uniformity in the composite material
- Ability to do mixes upwards of 600 percent faster than ribbon blending technology
- Reduced energy consumption per pound of material created
- The vessel jacket allows different media (hot oil, steam, or tempered water) to be used depending upon the thermal sensitivity of the product
- Ability to adjust between high pressure and low pressures, depending on the steps in the process
- Thermal jackets to allow for optimal temperature controls
- Easy to scale up and predict mix times after lab testing
- Vessels can be further outfitted to increase versatility:
- Mechanical seals –allows the vessel to be pressurized as well as reach a low vacuum (28 Hg)
- Liquid lances – allows media to be sprayed onto the substrate
Industries’ carbon fiber composites touch:
- Aerospace
- Reinforced polymers
- Textiles
- Reinforced Graphite
- Asphalt and concrete
- And many more
Processall maintains a fully equipped testing facility in Cincinnati, Ohio designed to provide customers with the data they need to develop their process, evaluate equipment, scale up, and identify the necessary equipment to maintain desired production volumes. We extend an open invitation to all potential customers to bring their products to our test center and get a “hands-on” experience with our technology and capabilities.
We also maintain a rental fleet that customers can utilize to do further testing at their facility or employ to minimize their startup costs for a new process.
Please feel free to contact us with all your material processing questions and our experienced industry professionals will help you find the right mixing solutions for your particular application.