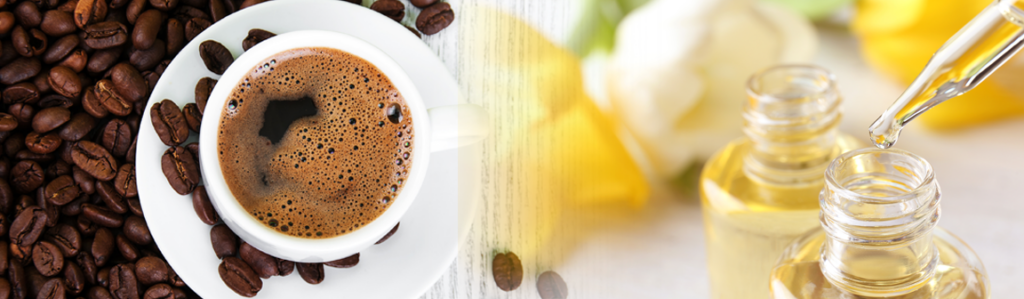
Flavor Extraction
The advantages ofthe MixMill process
The Processall Prestovac® Reactor is suitable for slurrying a leafy or fibrous product into a solvent to aid in removing all the flavors with minimum losses. With the Prestovac, the extraction takes place under pressure to help release all the flavors to the solvent.
Subsequently, the vapors are condensed and the slurry is either filtered in the Filt-A-Dry or pressed with a screw press. The slurrying process can be repeated to assure that all the flavors are captured. The final filter cake can then be vacuum dried to recover all the solvent prior to disposal.
The benefits of the Processall solvent extractions system:
• Better flavor yield due to enhanced mixing
and chopping.
• Extraction is carried out under pressure to
drive flavors out of the fibrous structure of the
bean or root.
• Multi-processing in one vessel, avoiding flavor
losses and expensive material transfer.
• Safer system with the self-contained vessel,
avoiding environmental exposure to solvents.
• The resulting filter cake can then be dried in the
same vessel by removing and recovering the
solvents. This will save disposal cost and allow
reuse of the solvent.
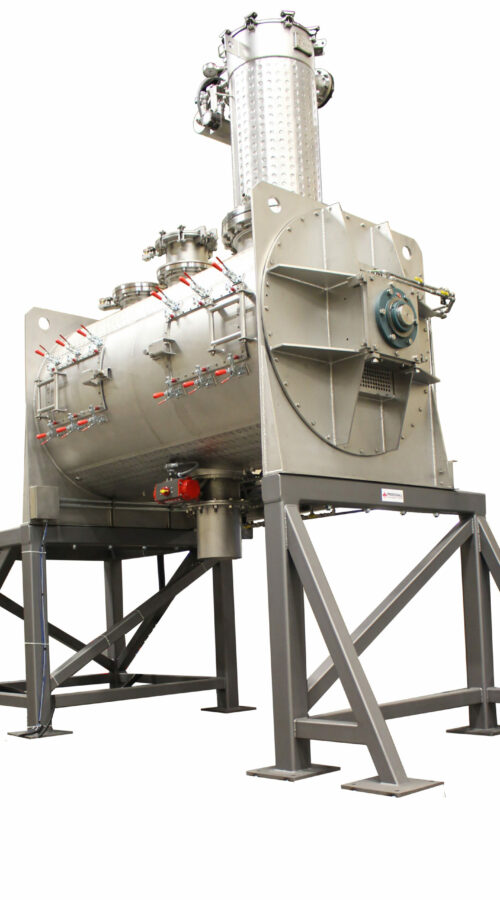
The Continuous Vacuum Dryer/Reactor is a horizontal mixing device with central shaft equipped with mixing elements perpendicular to the shaft. Multi-mixing elements in conjunction with adjustable weirs are provided to introduce the product through different processing zones for thermal treatment or conducting chemical reactions. The device incorporates a heating or cooling jacket.
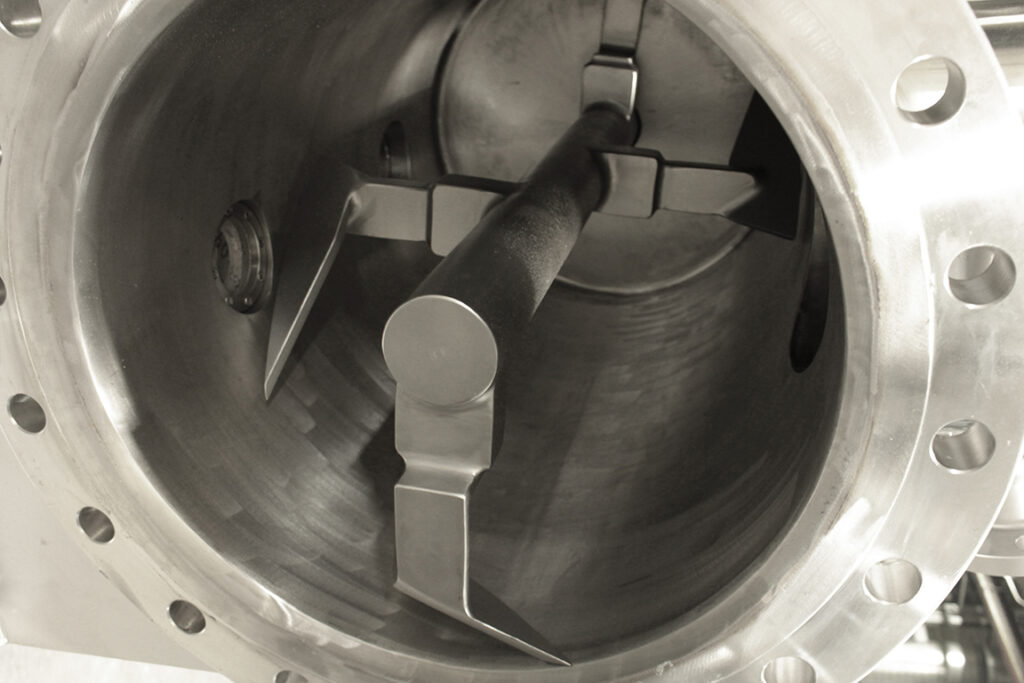
Mixing of Solids, Liquids & Fibrous Materials
Features:
• Plow/Mill or mixing elements provides thorough blending of materials and lower energy consumption since the cycle
times are considerably shorter.
• The mill shaft is equipped with special blades to aid the
opening of fibers and the dispersing of solids and resins.
They also minimize the formation of lumps.
• The mill shaft assembly is designed so it can be easily
maintained or replaced without changing the entire
electric motor.
• Shaft seals for the main and mill shaft can be standard
stuffing box, air seals, or double face mechanical seals for
long life and low maintenance.
• Liquid injectors are integral to the vessel and mounted
over the mill/disperser for maximum efficiency when
blending wet mixes.
• Mixing vessel can be jacketed for heating or cooling
to control product temperature. They can also be used in
conjunction with solvent recovery systems.
• All mixing elements, seals, and gasketing materials are
easily replaced.
• Local or remote mounted controls and microprocessors
can be supplied for the complete automation
of the process.