Since the 1950s children around the Cincinnati, Ohio market knew of this modeling clay called Play-Doh. Initially, Play-Doh was developed in the 1930s by Noah McVicker as a product to aid in wallpaper cleaning for Kroger. It was found to help to remove residual materials from wallpaper. However, as sales of the wallpaper cleaner diminished the McVicker’s family learned about a new market for this material from a relative who was a preschool teacher. She informed the family she had seen some of her students making art with this wallpaper cleaner. Therefore, the family immediately targeted a new market for this product which was modeling clay. The modeling clay market had been around for hundreds of years, but few people had ever targeted this material to children. The material became an immediate success with young children and the product quickly grew in popularity. The formulation was soon patented by McVicker’s upstart company Rainbow Crafts in 1958. Later Rainbow Crafts merged with the Cincinnati-based Kenner corporation as the material’s popularity continued to grow.
As a result of the instant success of Play-Doh, more corporations began to enter this emerging market. As the McVicker family hit continued to grow in popularity corporations needed to determine a faster way to produce the material. Additionally, more players started to enter the rapidly growing child modeling clay market. These market conditions required companies to invest in newer manufacturing methods to optimize production to keep up with demands. Companies across this industry quickly determined plow mixers to be effective methods of improving efficiencies. This is because in comparison to traditional ribbon blending plowshare mixers are upwards of four times faster in mixing these materials. Plow mixing technology is also one of the few mixing technologies capable of mixing materials at the high Viscosities people see with children’s modeling clay. Initially designed for the bakery industry plow mixers are capable of mixing materials up to 600,000 cPs which is just what the modeling clay industry needed to help improve production efficiency. With the high horsepower motors, the raw materials are easily able to disperse into paste form and it can also effectively distribute the food colors used in these pastes.
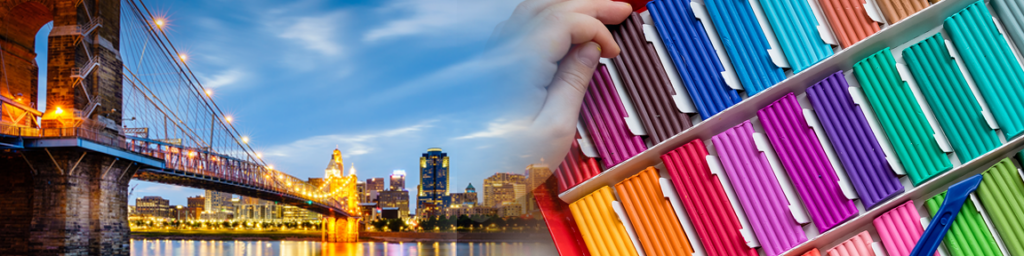
Processall’s plow mixing technology gives manufacturers a leg up on the competition. Listed below are some of the benefits of moving toward plow mixing technologies for food manufacturers.
- Creation of a mechanically fluidized bed that reduces the mixing time of the materials
- Dry powder blending applications have seen reductions of upwards of 500% in mixing times over other mixing applications
- Versatility because of its ability to mix powders, disperse pigment into liquid systems, and do hot melt blending all within one unit depending upon needs
- Mill breaks up clumps and can be used for defining particle size
- Thermal jackets to allow for optimal temperature controls
- High-speed mix which can handle materials as fine as dried oats without damaging the material
- Easy to scale up and predict mix times after lab testing
- Can be customized to include choppers
- Vessels can be further outfitted to increase versatility:
- Mechanical seals – will allow the vessel to be pressurized as well as reach a low vacuum (28 Hg)
- Liquid lances – allows media to be sprayed onto the substrate
- Ability to perform multiple unit operations in one unit resulting in:
- Faster throughputs
- Reduced energy consumption
- Smaller footprint on the production floor
- Less material handling and manpower
Unit Operations that Plow Mixing Combined to Aid in Modeling Clay Manufacturing
- Dry Powder Blending
- Powder Liquid Dispersion
- High Viscosity Mixing
- Dispersing Food Color
- And many more
Processall maintains a fully equipped testing facility in Cincinnati, Ohio designed to provide customers with the data they need to develop their process, evaluate equipment, scale up, and identify the necessary equipment to maintain desired production volumes. We extend an open invitation to all potential customers to bring their products to our test center and get a “hands-on” experience with our technology and capabilities.
We also maintain a rental fleet that customers can utilize to do further testing at their facility or employ to minimize their startup costs for a new process.
Please feel free to contact us with all your material processing questions and our experienced industry professionals will help you find the right mixing solutions for your application.