A metallic stearate is a compound composed of long-chain fatty acids combined with metals of different valences. Metal stearates can either be liquid or solid and are typically thought of as salt. Some of the most common metallic stearates are aluminum, calcium, magnesium, potassium, and zinc. Stearates are frequently applied as processing aids when utilizing acid-based reactions. They are commonly applied in the manufacturing of many different products such as plastic pipes, electrical insulation, vinyl siding, and even soap.
The application of metallic stearates provides processors with several sought-after properties when mixing product compounds. Benefits of these properties include lubrication, separation, water repellency, foam inhibition, gelling, and stabilizing effects during processing. In the plastic industry, metallic stearates are added to resin granules to provide lubrication and mold release in injections molds. The water repellent properties make it applicable in diverse fields such as cement, cosmetics, powder, and masonry treatments. Metallic stearates are used for calendaring, crystalline film, adhesives and sealants, ceramics, coated fabrics, medical devices, and roofing materials.
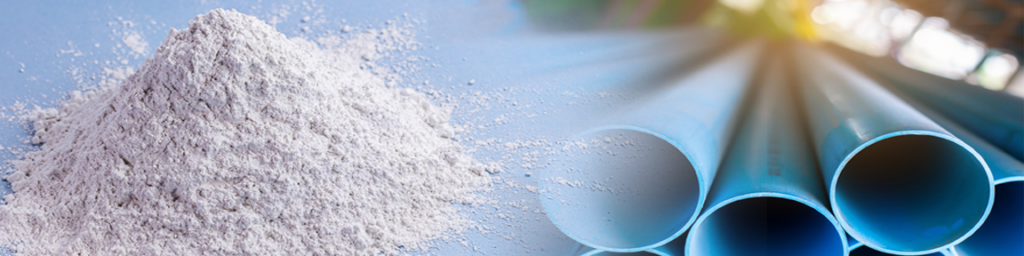
Below are several common examples of the diverse applications using metallic stearates:
- Plastic: Internal/external lubricants, processing aids for injection molding release
- Building and Construction: As hydrophobic agents, release agents, water repellent
- Foundry Industry: Core binder
- Animal Feeds: Mineral mixture additive
- Rubber: Anti-tackifier, lubricant, and mold release
- Pharmaceuticals: Tableting, anti-caking, compacting, mold release anti-agglomerate
- Powder Metallurgy: Flow-aid in sintering
- Wood Lacquers: As sanding aid
- Asphalt: Hardness modifier
- Cable Filling: Gelling agent, improved heat resistance
- Color Concentrate: Pigment wettability and dispersion
- Corrugated Board: Scuff and blocking resistance
- Paints: Settling, abrasion and scratch resistance, anti-blocking, water-repelling
Metal stearates are prepared through an acid-base reaction. In a typical metal stearate process, the ingredients are wetted and reacted with a base, with some metal stearate reactions performed under pressure. The byproducts are then filtered before drying the product. Historically, processors have used kettle reactors which involve multiple pieces of equipment to reach the end product. This type of processing is proven to be slow, inefficient, and environmentally unsafe. For these reasons, processors began looking for better ways to streamline these methods.
Through the use of a mechanically fluidized bed, plow mixers, reactors, and plow vacuum dryers are able to evenly combine, chemically react, and dry these reagents to create a free-flowing powder in a single batch process. The final product is sifted and packaged without requiring post-milling.
Processall recently completed the installation of a new unit for a client and almost immediately upon installation of this unit the client saw a 20% increase in production. This all while maintaining the same batch size over their previous plow mixing unit. This immediate improvement in production will greatly improve the customer’s bottom line. This is because business analysts project the metal stearate market will grow at a rate of 5-6% for at least the next 5 years. Plow mixing technology has been used by many leading metal stearates manufacturers for some time. The versatility of plow mixers enables manufacturers to reduce the footprint on the plant floor for this reaction while additionally reducing the energy consumption of the plant.
Processall has a long history of working with companies in the metal stearate market aiding in everything from initial testing to installation of the unit to maintenance throughout the life cycle of the unit.
Processall’s plow mixing technology gives manufacturers a leg up on the competition. Listed below are some of the benefits of moving toward plow mixing technologies for metal stearate applications.
- High heat transfer rate because of the creation of a mechanically fluidized bed within the drying vessel
- The vessel jacket allows different media (hot oil, steam, or tempered water) to be used depending upon the thermal sensitivity of the product
- A vacuum lowers the vapor pressure of the liquid, facilitating quicker drying times.
- Allows for the collection of liquids
- Mill breaks up clumps and can be used for defining particle size
- Thermal jackets to allow for optimal temperature controls
- High-speed mix which can handle materials as fine as dried oats without damaging the material
- Easy to scale up and predict mix and drying times after lab testing
- Ability to remove water or organic solvents from material
- Vessels can be further outfitted to increase versatility:
- Mechanical seals – will allow the vessel to be pressurized as well as reach a low vacuum (28 Hg)
- Liquid lances – allows media to be sprayed onto the substrate
- Ability to perform the reaction and the mixing and drying within one unit resulting in:
- Faster throughputs
- Reduced energy consumption
- Smaller footprint on the production floor
Types of Metal Stearates Processall has worked with
- Calcium Stearate
- Lithium Stearate
- Zinc Stearate
- Magnesium Stearate
- Sodium Stearate
- Lead Stearate
- Potassium Stearate
- And many more
Processall maintains a fully equipped testing facility in Cincinnati, Ohio designed to provide customers with the data they need to develop their process, evaluate equipment, scale up, and identify the necessary equipment to maintain desired production volumes. We extend an open invitation to all potential customers to bring their products to our test center and get a “hands-on” experience with our technology and capabilities.
We also maintain a rental fleet that customers can utilize to do further testing at their facility or employ to minimize their startup costs for a new process.
Please feel free to contact us with all your material processing questions and our experienced industry professionals will help you find the right mixing solutions for your application.