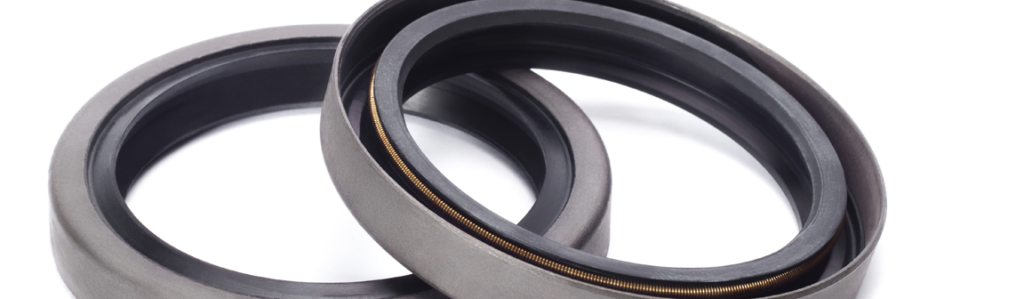
Mixing
of Solids, Liquids & Fibrous Materials
The advantages of the Mixmill process
The mixing of three different materials such as solids
or fillers, liquids or binding resins, and fibers or reinforcement with their diverse characteristics is one
of the most difficult processing steps to achieve.
Plow-type mixers, when equipped with mill/disperser mechanisms, have proven to be outstanding performers in the thorough blending of these three types of materials.
The mixing principle of these mixers is based on the rotation, within a confined vessel, of a shaft equipped with plow shape agitators. As plows pass through the mix, it produces a dividing, kneading action on the blended mass. This mixing action brings the three diverse materials of the mix in intimate contact with each other. The mixing action of the plows is augmented by high-speed mill/disperser. The plows constantly expose the mix to the high speed mills/dispersers. The dispersers intimately mix solid fillers and viscous resins throughout the batch. The mill also opens the fibers to reduce the density and expand their volume for maximum performance in the final product. If needed, the fibers can be opened or “pre-fluffed” in the mixer prior to the addition of the
solid and liquid ingredients. Once the mixing cycle is completed the mixer is discharged while running, which allows quick and complete discharge of the vessel.
Typical Applications:
• Brake Lining
• Clutch Facing
• Gasket Sheeting
• Phenolic Molding Compounds
• Polyester Molding Compounds
• Caulking Compounds

Features:
• Plow/Mill or mixing elements provides thorough
blending of materials and lower energy consumption since the cycle times are considerably shorter.
• The mill shaft is equipped with special blades to aid the opening of fibers and the dispersing of solids and resins. They also minimize the formation of lumps.
• The mill shaft assembly is designed so it can be easily maintained or replaced without changing the entire electric motor.
• Shaft seals for the main and mill shaft can be standard stuffing box, air seals, or double face mechanical seals for long life and low maintenance.
• Liquid injectors are integral to the vessel and mounted over the mill/disperser for maximum efficiency when blending wet mixes.
• Mixing vessel can be jacketed for heating or cooling to control product temperature.
They can also be used in conjunction with solvent recovery systems.
• All mixing elements, seals, and gasketing materials are easily replaced.
• Local or remote mounted controls and microprocessors can be supplied for the complete automation of the process.