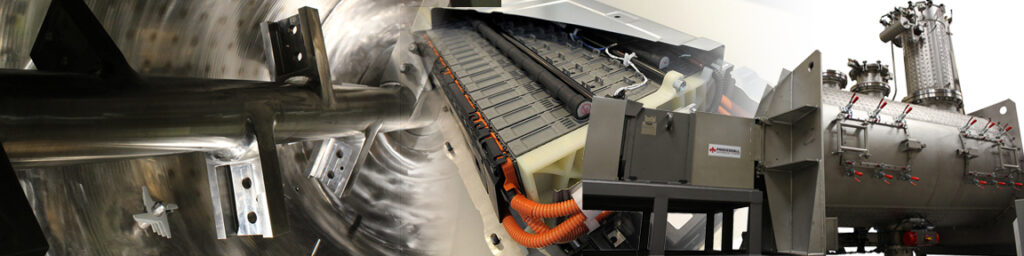
James Woolsey who was the former head of the CIA under Bill Clinton once said, “We aren’t addicted to oil, but our cars are.” Yes, that statement may have held true for many years but with the huge advancements in battery technologies that statement is becoming a thing of the past. In June of 2023, Toyota announced to the world that they have now created a battery that is projected to power cars for upwards of 700 miles and it is able to be recharged in 10 minutes. Due to this announcement and many other recent scientific advancements in battery technology, the race toward EV powered automobiles is on.
Still the idea of battery powered machines goes all the way back to the time of the American Founding fathers. Benjamin Franklin himself designed one of the first electric motors but the motor was limited in power and therefore was castoff into the dust bin of history. Still, Franklin’s motor generated enough power to turn a turkey rotisserie. That being said this did not deter the human spirit from continuing to develop this technology and apply it to motorized vehicles. In April of 1881, the French inventor Gustave Trouvé drove what many individuals believe to be the first electric car down the streets of Paris. Although this and many other early motorized carriages helped spur the automotive industry of today, this early battery technology was replaced with the internal combustion engine for much of the 20th Century.
This is because internal combustion engines provided more speed and range than the early battery powered vehicles. For this reason, little research in this field continued for some time. Most work done after this point on battery powered vehicles was limited to developing vehicles that could work in areas the internal combustion engine could not work. As the decades progressed automakers began to dabble back into EV technology as a possible alternative to internal combustion engines. Still, little work was done on making EV powered automobiles. It was not until Toyota shocked the market with the Toyota Prius in 2000 that all this changed. This hybrid vehicle immediately became a commercial success and showed the world that battery powered technology is indeed the wave of the future. 6 years later, Elon Musk supercharged the world of EV with the unveiling of the Tesla Roadster. Not only did the car look cool but it also was fast and had people enamored with what EV vehicles could do. After the commercial success of both these vehicles, many auto manufacturers have begun to pivot hard into the realm of EV.
As many companies are finding with this hard pivot to EV manufacturing, it is much different than working with the internal combustion engine. EV batteries present many unique challenges to automakers finally dipping their toes into this market. One of the biggest challenges many auto makers are encountering is they are now at the whims of the chemical industry. The Chemical industry can often be prone to supply chain disruptions due to lack of chemical raw materials. It is for this reason companies like General Motors and many more are teaming up with companies in the battery industry to now make their own batteries.
Still, this is presenting its own unique challenges as well. Many battery manufacturers have had issues in the past with getting a proper consistent mix of materials. However, many battery makers recently discovered that plow mixers can eliminate this once constant problem. This is because plow mixers operate under the idea of a mechanically fluidize bed. This means they are able to mix the material at an extremely high rate of speed giving the Mixers High Froude numbers. (Froude number is a dimensionless number that relates materials velocity when being mixed to a vessel’s diameter.) Plow mixers have been used by many metal blending operations prior to their recent adoption as the mixer of choice for battery makers. Due to the high Froude number, this technology has historically demonstrated the ability to mix metal powders together in a way that other powder mixer technologies can only dream of achieving.
Plow mixers have also been used in other parts of the manufacturing process of EV. It is not uncommon for some EV battery makers to equip their plow mixers with injection ports. This is to enable the addition of liquids into the vessel to mix the material with the already mixed metal powders creating a pasty dispersion. It is often hard for other mixers to handle these high viscosity materials created during this phase of product and often takes other mixing technologies much longer to adequately mix in the material. Speed of production is something critical to companies in the automotive supply chain. One recent Forbes article stated auto plants lose on average $22000 per minute a plant is down. Therefore, eliminating any potential bottleneck point is vital to any automotive supplier or manufacturers.
Another area of bottleneck that plow mixing technology has helped the battery industry eliminate on a consistent basis is the long drying times. The battery making process often requires drying after chemical treatments occur to the anode and cathodes in the process. It is not uncommon for battery manufacturers to need their battery anode or cathode to be at moisture contents below 1% which can take many drying technologies long times to achieve. Plow Mixers with Vacuum dryers have been found to have some of the fastest drying times on the market. It is not uncommon for plow mixer dryers to achieve U factors (thermal transmittance) of over 40 BTU/(Hr-ft²-°F). For drying applications plow mixers are equipped with both a heated jacket and a vacuum system enabling drying to occur faster. The low vacuum pressures reduce the overall boiling point of materials. (See chart 1 for how vacuum pressures can affect the boiling point of water.) Additionally having a difference in the temperature of the boiling point of the material and the temperature of the jacket heated material effects the logarithm mean temperature. The higher the difference between these 2 numbers the more thermal transference can occur. Finally, because the material is being mixed by the plows inside the mixer this enables the material to be able to touch more heated surfaces and therefore helps to facilitate more heat transfer.
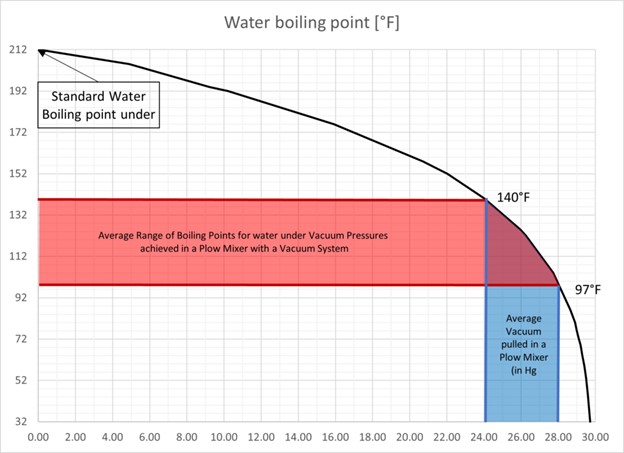
In addition to being able to operate under negative vacuum pressures, plow mixers can also be designed to operate under positive pressures as well. This ability to operate under both positive and negative pressure make them also an ideal candidate to serve as reaction vessels for the battery industry. Whether it be for the refining of the raw materials after being mined or general reactions in the battery making process, plow mixers have consistently demonstrated the ability to serving as a U1 pressure vessel for these applications.
Besides the previously discussed unit operations, plow mixers can do other unit operations for battery makers. This is because they have the ability to be equipped with accessories like spray nozzles that can atomize the coating solution and ensure the material adequately encapsulates the material needing these coatings. The coating does not even need to be a low viscosity material because plow mixers can be customized to include chopper systems which are high speed secondary motors. These chopper systems have demonstrated the ability to be used for spraying materials that are high viscosity liquids. (See the image below for a more in-depth explanation of how spray systems work in plow mixers.)
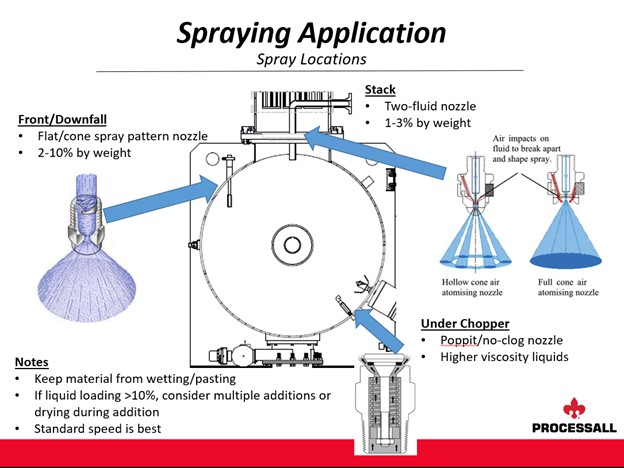
However, choppers themselves are not limited to just coating. They can also be used in operations like drying, agglomeration and granulation. Still, it is important to always do testing with experienced lab personnel prior to purchasing this accessory because sometimes operations do not need this option.
Processall’s Plow Mixing technology gives the battery industry a leg up on the competition. Listed below are some of the benefits of moving toward plow mixing technologies for Battery manufacturers.
- Creation of a mechanically fluidized bed which reduces the mixing time of the materials.
- Dry powder blending applications have seen reductions of upwards of 2,000% in mixing times over other mixing technologies.
- The vessel jacket allows different media (hot oil, steam, or tempered water) to be used depending on the thermal sensitivity of the product.
- Versatility because of its ability to mix powders, disperse pigment into liquid systems, and do hot melt blending all within one unit depending upon needs.
- Reductions in drying times up to four times faster than other technologies on the market
- Mill breaks up clumps and can be used for defining particle size.
- Thermal jackets to allow for optimal temperature controls.
- High-speed mix which can handle materials as fine as dried oats without damaging the material.
- Easy to scale up and predict mix times after lab testing.
- Able to be made a U1 Pressure vessel.
- Vessels can be further outfitted to increase versatility:
- Mechanical seals – will allow the vessel to be pressurized as well as reach a low vacuum (28 Hg)
- Liquid lances – allows media to be sprayed onto the substrate.
- Ability to perform multiple unit operations in one unit resulting in:
- Faster throughputs
- Reduced energy consumption
- Smaller footprint on the production floor
- Less material handling and staffing
Processall maintains a fully equipped testing facility in Cincinnati, Ohio designed to provide customers with the data they need to develop their process, evaluate equipment, scale-up, and identify the necessary equipment to maintain desired production volumes. We extend an open invitation to all potential customers to bring their product to our test center and get a “hands on” experience with our technology and capabilities.
We also maintain a rental fleet that customers can utilize to do further testing at their facility or employ to minimize their startup costs for a new process.
Please feel free to contact us with all your material processing questions and our experienced industry professionals will help you find the right mixing and reacting solutions for your particular application.