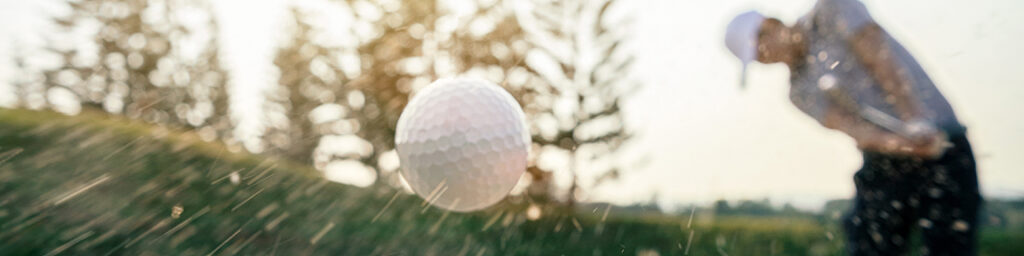
Best-selling author and world-renowned sports psychologist Dr. Bob Rottella best described golf this way, “Golf is not a Game of Perfect.” As any golfer will tell you no matter how good a golfer is, it is sometimes impossible to predict exactly what that little white ball will do after it has been hit. No matter how good a golfer may be, a myriad of things can still affect the trajectory of the golf ball. These factors can include everything from the person’s stance, grip, and swing plane. A minor deviation in any of those factors can change a ball from a perfect shot to a dreaded whiff. No matter how good a golfer you may be, golf balls sometimes just appear to have a mind of their own.
For this reason, millions in research dollars continue to be dumped into the golf industry and it has evolved into a 27.2-billion-dollar industry in the United States alone. Companies are continuously doing research on everything from better club design to golf ball design to help better the game for everyone. In fact, most average golfers are willing to spend big money in the hopes of shaving 1-2 strokes from their game. For this reason, it is not uncommon to see people spending $400-500 on a driver or $50-60 on golf balls in the hopes of improving their own game. The problem that arises is everyone’s golf game is different. Whether it be the hackers out with buddies on a Saturday morning on their second round of beers or Brooks Koepka playing to win the PGA Championship at Oak Hill County Club, every golfer needs something specially tailored to fit their game.
To help golfers improve their games the golf industry like many before it has evolved into a market of mass customization. Everything from golf clubs to golf balls are uniquely designed for different target audiences. Much like people previously paying money for golf club fitting services, retail stores are now offering golf ball fitting services to golfers. This is because of the wide variety of golf balls now available on the market. If you ask a handful of golfers what balls they prefer to play you will get a litany of different answers and that is because of the different properties each golf balls give. Some balls can give a 20-30 yards difference on a drive alone. Other balls are designed specifically to land on the green and just bite and give backspin. What the golf ball is designed to do can greatly affect the shot selection of a golfer. The proper decision on which golf balls to use can legitimately make or break some people’s rounds.
Due to the proprietary nature of business, each manufacturer uses different methods to construct what they envision to be their ideal ball for the golf market. Every golf ball maker uses different formulas for their golf balls, and it requires completely different manufacturing processes to complete. Just on the outer shell of the golf ball everything from the size of the dimples, design of the ball, and number of dimples can greatly affect everything from the drag coefficient to the path the golf ball will take. Additionally factors such as the materials of construction and structure of the inside golf ball can vary greatly. Some manufacturers use a single material for construction of the golf ball while others use upwards of 5 different materials. This variety of factors can all effect stuff like the spin and compression of a golf ball.
However, it has been shown all these processes can benefit from plow mixing technology. This is because plow mixers are one of the few mixers on the market capable of mixing materials at the high viscosities these materials encounter before the material is eventually cured. Plow mixers have repeatedly demonstrated the ability to handle liquids at the viscosity of 30,000 cPs. In fact, previous tests have shown the ability of plow mixers capable of mixing carbon fibers and or metal powders into materials like uncured rubber and thermoplastics which some golf ball makers are currently doing already.
Processall’s Plow Mixing technology gives golf ball makers and general chemical industry manufacturers a leg up on the competition. Some of the benefits of moving toward plow mixing technologies for chemical manufacturers include:
- Creation of a mechanically fluidized bed which reduces the mixing time of the materials
- Dry powder blending applications have seen reductions of upwards of 2,000% in mixing times over other mixing technologies
- Vessel jacket allows different media (hot oil, steam, or tempered water) to be used depending on the thermal sensitivity of the product
- Versatility because of its ability to mix powders, disperse pigment into liquid systems, and do hot melt blending all within one unit depending upon needs
- Reductions in drying times up to four times faster than other technologies on the market
- Mill breaks up clumps and can be used for defining particle size
- Thermal jackets to allow for optimal temperature controls
- High-speed mix which can handle materials as fine as dried oats without damaging the material
- Easy to scale up and predict mix times after lab testing
- Able to be made a U1 Pressure vessel
- Vessels can be further outfitted to increase versatility:
- Mechanical seals – will allow the vessel to be pressurized as well as reach a low vacuum (28 Hg)
- Liquid lances – allows media to be sprayed onto the substrate.
- Ability to perform multiple unit operations in one unit resulting in:
- Faster throughputs
- Reduced energy consumption
- Smaller footprint on the production floor
- Less material handling and staffing
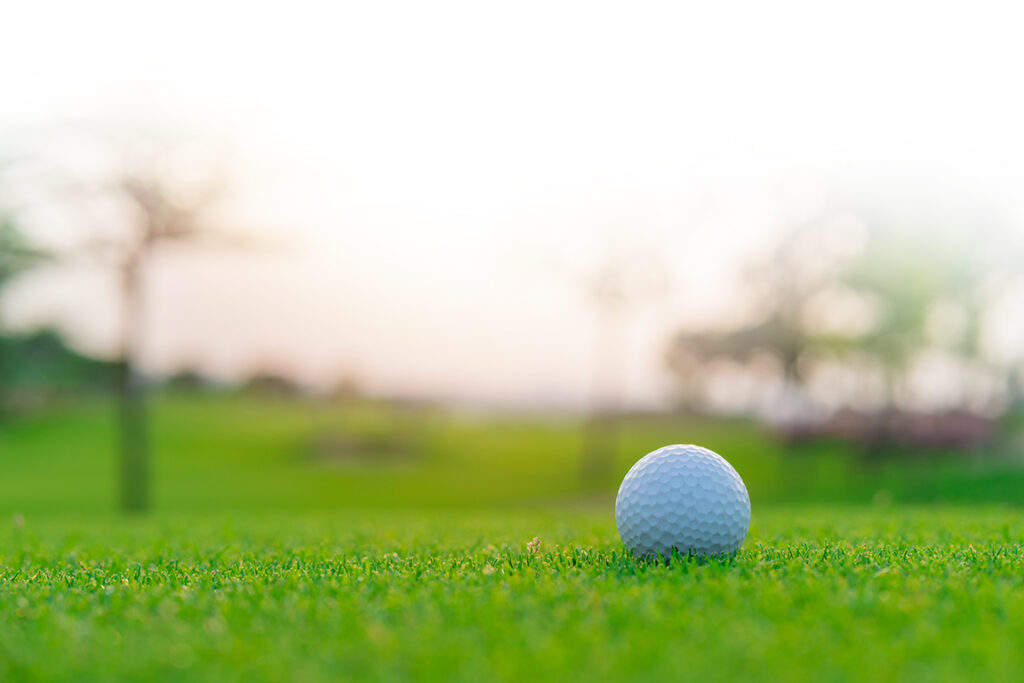
Processall maintains a fully equipped testing facility in Cincinnati, Ohio designed to provide customers with the data they need to develop their process, evaluate equipment, scale-up, and identify the necessary equipment to maintain desired production volumes. We extend an open invitation to all potential customers to bring their product to our test center and get a “hands on” experience with our technology and capabilities.
We also maintain a rental fleet that customers can utilize to do further testing at their facility or employ to minimize their startup costs for a new process.
Please feel free to contact us with all your material processing questions and our experienced industry professionals will help you find the right mixing solutions for your particular application.