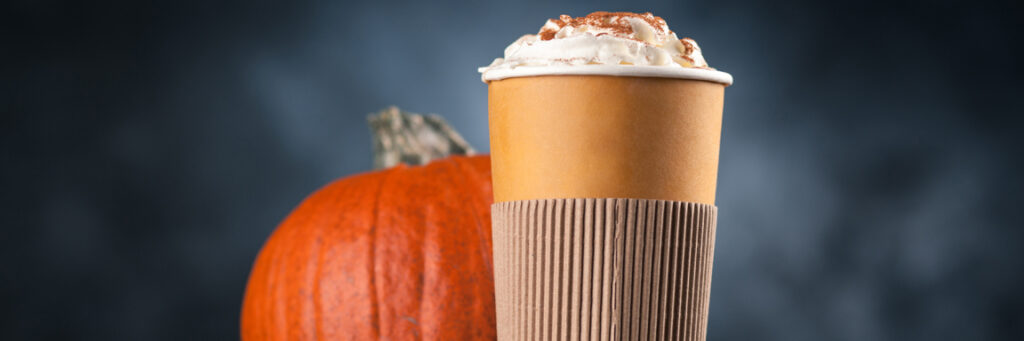
In 2003, Starbucks began top secret work to develop a new fall seasonal drink following their earlier successful holiday drink launches. The plan of Peter Dukes and his team was to make a drink centered around pumpkin. What the team eventually did was develop their own blend of herbs and spices similar to the spices used in pumpkin pie to create their version of the flavor people had been calling pumpkin spice.
Pumpkin Spice flavoring now is over a 6 billion dollars industry according to a recent Forbes article. In fact, in 2022 it was reported Americans are now consuming 236 million dollars on just pumpkin spiced grocery items, a 24% increase over the previous year. Today, pumpkin spice favoring is used in everything from drinks to baking to pet foods and even soaps.
Due to the high demand for this seasonal spice blend companies need to investigate new methods to optimize their production. One of the technologies that has utilized by the spice market is plow mixer technology. This is partly because of the Froude number (a dimensionless number used to measure speed in relation to other factors) at which the plow mixers operate. They also have demonstrated the ability to mix in many materials other blending technologies cannot do. Not only do these mixers have large motors but they can also be accessorized with chopper systems to which rotate at 3600 RPM to mix and disperse in problematic materials.
Since some spice blending has now evolved into culinary blending, the usage of syrups to give flavors is being commonly employed instead of just dry spice blending. Some spice blenders are now creating liquid syrup mixtures instead of dry powders. The popularity of liquid syrups has increased as baristas and home customers share fall drink recipes on social media. For this reason, some syrup manufacturers have decided to use plow mixer technologies when making materials like maple or pumpkin syrups. This due to the mixers high U factors (rate of heat transfer) these machines demonstrate when operating as a dryer. It is not uncommon to see values over 40 BTU/(Hr-ft²-°F).
Processall’s Plow Mixing technology gives spice makers and general food and beverage industry manufacturers a leg up on the competition. Listed below are some of the benefits of moving toward plow mixing technologies for chemical manufacturers.
- Creation of a mechanically fluidized bed which reduces the mixing time of the materials
- Dry powder blending applications have seen reductions of upwards of 2,000% in mixing times over other mixing technologies
- The vessel jacket allows different media (hot oil, steam, or tempered water) to be used depending on the thermal sensitivity of the product
- Versatility because of its ability to mix powders, disperse pigment into liquid systems, and do hot melt blending all within one unit depending upon needs
- Reductions in drying times up to four times faster than other technologies on the market
- Mill breaks up clumps and can be used for defining particle size
- Thermal jackets to allow for optimal temperature controls
- High-speed mix which can handle materials as fine as dried oats without damaging the material
- Easy to scale up and predict mix times after lab testing
- Able to be made a U1 Pressure vessel
- Vessels can be further outfitted to increase versatility:
- Mechanical seals – will allow the vessel to be pressurized as well as reach a low vacuum (28 Hg)
- Liquid lances – allows media to be sprayed onto the substrate.
- Ability to perform multiple unit operations in one unit resulting in:
- Faster throughputs
- Reduced energy consumption
- Smaller footprint on the production floor
- Less material handling and staffing
Processall maintains a fully equipped testing facility in Cincinnati, Ohio designed to provide customers with the data they need to develop their process, evaluate equipment, scale-up, and identify the necessary equipment to maintain desired production volumes. We extend an open invitation to all potential customers to bring their product to our test center and get a “hands on” experience with our technology and capabilities.
We also maintain a rental fleet that customers can utilize to do further testing at their facility or employ to minimize their startup costs for a new process.
Please feel free to contact us with all your material processing questions and our experienced industry professionals will help you find the right mixing solutions for your particular application.