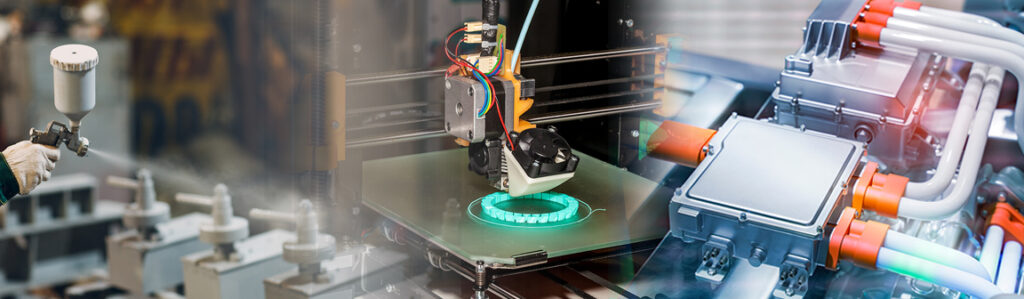
Metallic powders blending is crucial to many industries today. These blends touch everything from powder forging, 3D printing, battery production, and industrial coatings. As a result, metal powders mixing is continuing its growth annually at a pace of 6%. If current trends continue it will become an 8.5-billion-dollar industry in 5 years. Although the blending operation is simple, few pieces of equipment exist in the market that can adequately mix these materials due to their often heavy weights and densities.
One of the few technologies capable of doing this mixing is a plow mixer because it creates a mechanically fluidized bed in the mixing vessel. It is for this reason plow mixing technology has quickly become the prominent mixing technology to companies in this industry. The most cited reason corporations use them is these mixers have the high horsepower motors needed to speed up mixing time without effecting the quality of the mix. Plow mixing technology has been found to increase blending speed upwards of 300% versus ribbon blending technology. Additionally, the mixer is fully customizable to fit clients’ individual needs. They have the capability of performing multiple unit operations concurrently or in stages as part of an individual program. Common options companies select to customize their individual mixer to fit their individual processes are:
- Liquid lances and spray nozzles which enable particle coating operations to occur
- Chopper blades which help disperse materials and control particle sizes for the final product
- Optional Vacuum systems used to remove unnecessary fluids in the mix
- Vent stacks with optional pulse back filters to prevent material from leaving
Processall’s plow mixers are always designed with the customer’s input to insure it fits their specialized needs. Since many metallic blends require a coating step in the process, one of the most common designs for these systems is to have it both coat the material with liquid solutions and then subsequently dry the material as well. Plow mixers can do the coating operation while mixing and then evaporate the unused material. This is done through usage of both a vacuum system and a heat transfer jacket that has a heat transfer fluid in it to heat up the vessel. Together with these features, plow mixers become the fastest drying systems on the market. This is because the fast-mixing action of the unit enables the material to have heat transfer occur with all areas of the jacket. Some customers have seen dry times of 1 hour or less with these units. Additionally, plow mixers have even been used in several agglomeration type operations in metal powder blending.
Processall’s plow mixing technology gives manufacturers a leg up on the competition. Some of the benefits of moving toward plow mixing technologies for metal powder manufacturers are:
- Creation of a mechanical fluidized bed which reduces the mix time of the materials
- Dry powder blending applications have seen reductions of upwards of 300% in mixing times over other types of mixers
- Vessel jacket allows different medias (hot oil, steam, or tempered water) to be used depending upon thermal sensitivity of product
- Versatility because of its ability to mix powders, disperse pigment into liquid systems, and do hot melt blending all within one unit
- Reductions in drying times 4 times faster other technologies on the market
- Mill breaks up clumps and can be used for defining particle size.
- Thermal jackets to allow for optimal temperature controls
- High speed mix which can handle materials as fine as dried oats without damaging the materials
- Easy to scale up and predict mix times after lab testing
- Able to be made a U1 Pressure vessel
- Vessels can be further outfitted to increase versatility:
- Mechanical seals – will allow vessel to be pressurized as well as reach low vacuum levels.
- Liquid lances – allows media to be sprayed onto substrate
- Ability to perform multiple unit operations in one unit resulting in:
- Faster throughputs
- Reduced energy consumption
- Smaller footprint on the production floor
- Less Material handling and manpower
Current and potential uses of plow mixers in metal powders:
- Battery blending
- Metal powder dispersions
- Iron ore agglomeration
- Evaporation and removal of residual materials
- Metal coatings
- And many more
Processall maintains a fully equipped testing facility in Mason, Ohio designed to provide customers with the data they need to develop their process, evaluate equipment, scale-up, and identify the necessary equipment to maintain desired production volumes. We extend an open invitation to all potential customers to bring their product to our test center and get a “hands on” experience with our technology and capabilities.
We also maintain a rental fleet that customers can utilize to do further testing at their facility or employ to minimize their startup costs for a new process.
Please feel free to contact us with all your material processing questions and our experienced industry professionals will help you find the right mixing solutions for your particular application.