Covid 19 taught the world one thing, it is even if the world is shut down, alcohol is an essential part of the American economy. In fact, liquor stores were deemed essential businesses in most states during the pandemic. Now plow mixing itself is not a technology that can affect the centuries-long process of fermentation of grains into alcoholic beverages, but it is a technology that has been used by some to make the alcohol industry itself a greener industry.
Plow mixing technology has touched most areas in the alcohol industry enabling it to become a very green industry with a high level of reusing of materials. The spent mash is often dried and reprocessed for animal feeds. Reclamation of spent mash has been common in the alcohol industry for a long time; still, it is often hard to effectively convert all the spent grains into animal feeds. Companies across the alcohol industry have been working with plow mixing manufacturers on methodologies to effectively do this. One of the most common tactics they have tried is mixing and drying the spent grains with a proprietary mixture to lengthen the usability of these grains. The feed is then consumed by livestock and through biological processes, they create manure which can be treated and converted into fertilizers inside plow mixers. The fertilizers are then applied to next year’s grains so they can help the grains grow.
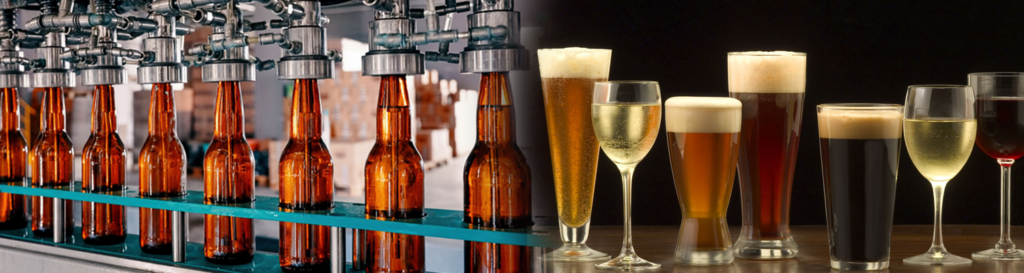
Other green applications in the alcohol industry involve the manufacture and transport of yeast. It is done by removing any excess water from yeast after it is grown, it is common for many yeast manufacturers to dry yeasts into dormant yeast powders. Many yeast suppliers use plow mixing technologies to do this drying because the dryers are thermally sensitive, and have a great heat transfer coefficient. Plow dryers are also gentle enough to not damage the yeast itself. This low water content enables yeast makers to have lower transportation costs helping the overall supply chain’s bottom line.
Processall employees have a long history of working with companies in all markets, aiding in everything from initial testing to installation of the unit to maintenance throughout the life cycle of the unit.
Processall’s plow mixing technology gives manufacturers a leg up on the competition. Listed below are some of the benefits of moving toward plow mixing technologies for the alcohol industry:
- High-speed and a shorter mix time, which reduces the energy per pound of material
- Creation of a mechanically fluidized bed which reduces the extraction times
- High-heat transfer rate within the vessel enables faster drying
- The vessel jacket allows different media (hot oil, steam, or tempered water) to be used depending upon the thermal sensitivity of the product
- Adjustable pressure conditions that enable both high-pressure applications and near-vacuum pressures to occur during different stages of the reaction
- Allows for the collection of volatilized liquids
- Mill breaks up clumps and can be used for defining particle size
- Ability to serve as a reaction vessel to convert biological waste products into fertilizer
- Thermal jackets to allow for optimal temperature controls
- High-speed mix which can handle materials as fine as dried oats, without damaging the material
- Easy to scale up and predict mix drying times after lab testing
- Vessels can be further outfitted to increase versatility:
- Mechanical seals – allow the vessel to be pressurized as well as reach a low vacuum (28 Hg)
- Liquid lances – allow the media to be sprayed onto the substrate
- Ability to perform the reaction, mixing, and drying within one unit resulting in:
- Faster throughputs
- Reduced energy consumption
- Smaller footprint on the production floor
Ways plow mixers make alcohol a Greener Technology
- Converting spend malt into livestock feed
- Reacting sodium hydroxide with manure to produce natural fertilizers
- Drying of yeast to reduce energy costs for transport
Processall maintains a fully equipped testing facility in Cincinnati, Ohio designed to provide customers with the data they need to develop their process, evaluate equipment, scale up, and identify the necessary equipment to maintain desired production volumes. We extend an open invitation to all potential customers to bring their products to our test center and get a “hands-on” experience with our technology and capabilities.
We also maintain a rental fleet that customers can utilize to do further testing at their facility or employ to minimize their startup costs for a new process.
Please feel free to contact us with all your material processing questions and our experienced industry professionals will help you find the right mixing solutions for your particular application.