Drying touches many aspects of product manufacturing. Whether it be food, pharmaceutical, chemical, or agrochemical industry, drying technologies are a vital part of the production because many processes result in forming a wet filter cake. This cake must be dried before further processing can be conducted.
Various drying techniques exist on the market, like air driers, microwave driers, radiant heat driers, and vacuum driers. However, few offer the speed, particulate size control, and customization features of plowshare vacuum driers. The plowshare vacuum driers are a cylinder located on its side with a central shaft having mixing elements or Plows. The spinning of this shaft and plows creates a mechanically fluidized bed. The mixing action creates a maximum heat transfer rate. The mixing action also continually exposes more new particles to the surface area for vapor removal as agglomerates or lumps are reduced in size. The vessel is additionally put under a vacuum to reduce the boiling points of solvents and reduce the chances of degradation for heat-sensitive materials. The lowered boiling point also limits the needed product temperature, which protects the chemical purity by heating the drum to the lower temperatures required to achieve vaporization at low pressure. The vacuum also helps create a path for the liquid to leave the drying vessel and provides a route to recover the solvents. Due to the combination of these factors, the material achieves quicker drying times because of the high level of surface contact with the vessel’s shell during drying. (See Fig 1 for an overview of the parts)
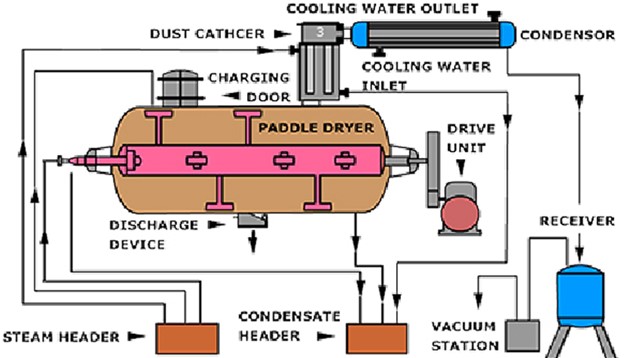
Many companies use plowshare vacuum dryers to evaporate these residual solvents. Vacuum drying with plow mixer technology maximizes the heat transfer coefficient between the jacket and the product while lowering the product temperatures required for vaporization. See Figure 2 for an example of how much lower the boiling point is under Vacuum conditions. (24 in Hg and 28 in Hg are typical vacuum pressures one can achieve in plow mixer vacuum driers)
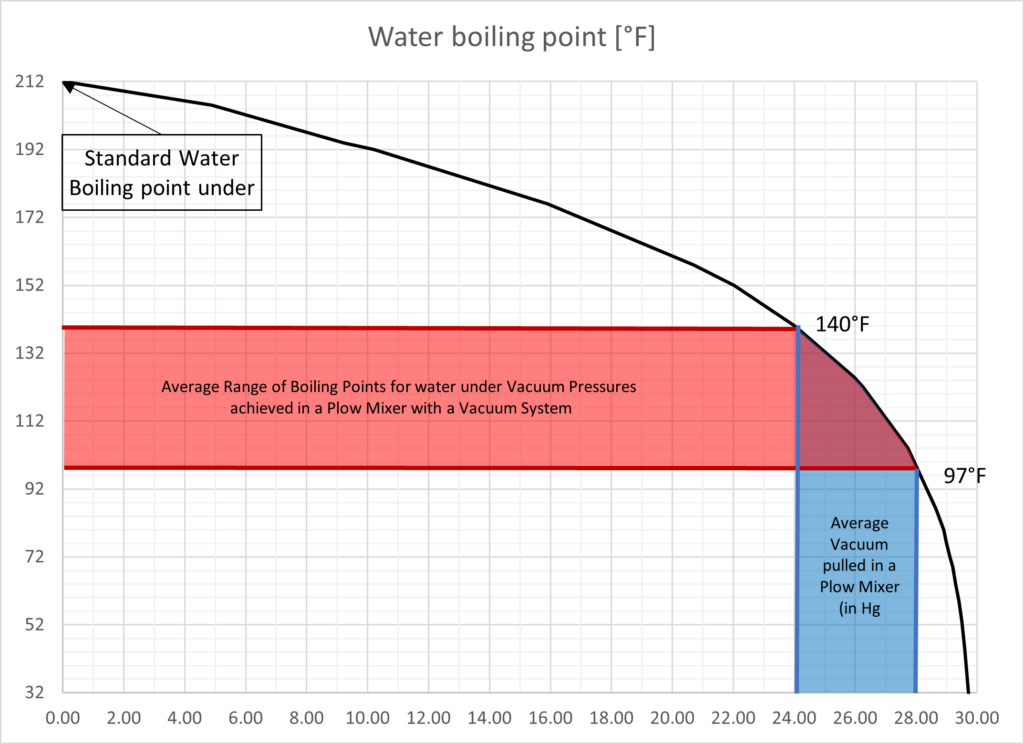
The vacuum dryer agitation also helps to eliminate or reduce the amount of agglomerated product, assuring complete dryness and a narrower particle size distribution. While drying, materials may go through a heavy or doughy phase where large lumps are generated. Occasionally, these larger lumps hinder the drying rate because the liquid being removed must travel to the surface of these lumps. Due to the fact agglomerations can occur, plowshare vacuum driers can be equipped with additional mixing devices called choppers that can impart shear to break up the large, heavy lumps. They can break apart any agglomerates and help reduce the product particle size. (See Figure 3).
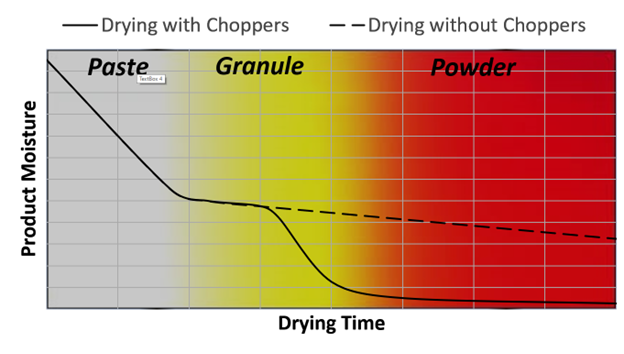
Still, most of the time plows, high-speed agitation alone prevents particulate agglomeration from occurring and avoids the need for chopper technology. It is best to do laboratory testing with trained technical personnel to determine the best course of action when performing drying applications.
After reaching the final desired volatile content in the product, the material can be cooled for collection and final packaging without exposing the operator to dangerous conditions. Cooling the product can also reduce the risk of fire or explosion by exposing the product to the atmosphere. The vacuum dryer can also be purged with an inert gas to protect the product and the operator if the removed liquid is a flammable solvent.
Processall’s Plow Mixing technology gives chemical manufacturers a leg up on the competition. Below are some benefits of moving toward plow mixing technologies for chemical manufacturers.
- The high heat transfer rate, which increases the speeds of drying
- Lower vaporization temperatures protect thermally sensitive material
- Customized with a wide variety of safety features to improve employee safety when handling dangerous materials
- Ability to serve as both a reactor and dryer of materials, thus reducing the need for multi-unit operations. (Many stearate manufacturers use plow mixers because of these features)
- VFD motors enable comprehensive levels of control for the mixer speed, therefore better control of the particle size of the dried material
- Customized to include pulse back filters for dust control
Processall maintains a fully equipped testing facility in Cincinnati, Ohio. It is designed to provide customers with the data they need to develop their process, evaluate equipment, scale up, and identify the necessary equipment to maintain desired production volumes. We invite all potential customers to bring their products to our test center and get a “hands-on” experience with our technology and capabilities.
We also maintain a rental fleet that customers can utilize to do further testing at their facility or to minimize their startup costs for a new process.
Please get in touch with us with all your material processing questions, and our experienced industry professionals will help you find the right mixing solutions for your particular application.